Micro Tech, Macro Effect
Shrinking a 30-pound gas analyzer to a wearable badge
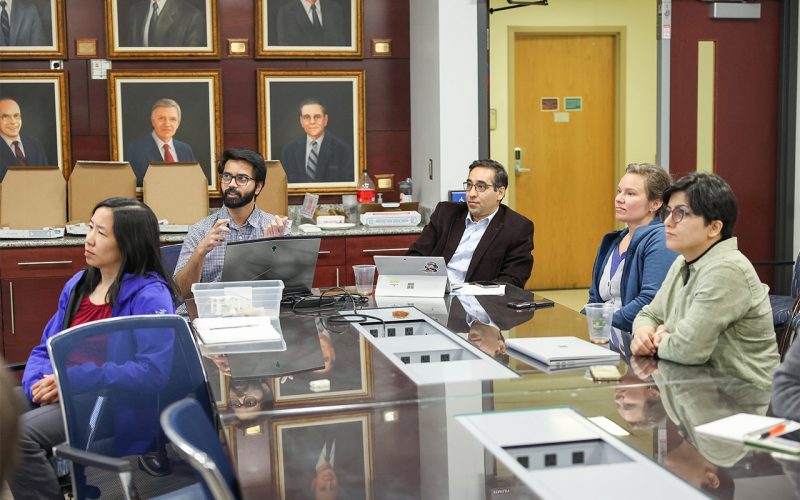
Each of us is exposed to thousands of chemicals daily. Most are harmless. Some are not. Knowing when we’re exposed to harmful chemicals is vital for workplace safety, but monitoring efforts are hampered by the large size of the technologies typically needed to detect these chemicals.
The gold standard for detecting what’s in the air we breathe is gas chromatography (GC)—an analytical method for determining the chemical composition of a gas using a device that runs gases through several meters of a capillary tubing known as a separation column. The size and expense of conventional GC equipment, however, present a challenge when trying to analyze in real-time, as does the time-consuming process of sending samples to a lab.
The solution, according to ECE Professor Masoud Agah, is a portable and/or wearable micro-GC, which combines a variety of different technologies. Over the last 17 years, his teams have made numerous advances to miniaturize GC technology and to develop new GC architectures. GC suitcase-sized equipment typically weighs 30 pounds or more. “We want to make something you can wear, without noticing the weight,” he says.
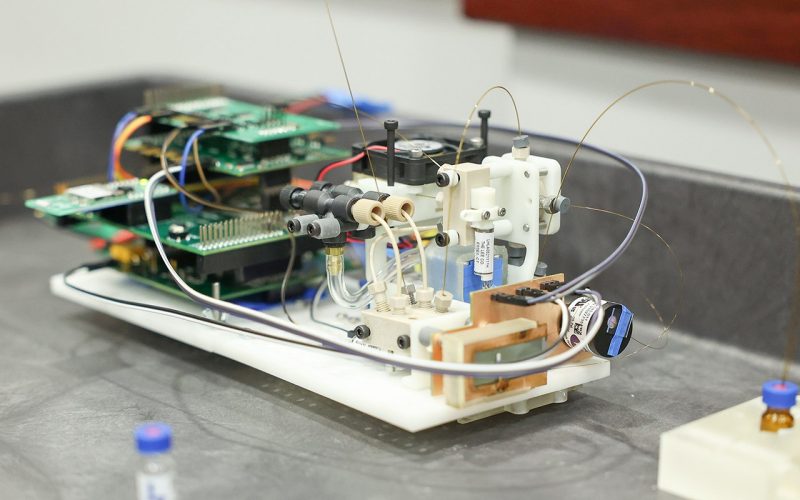
Today, Agah and co-investigators from across the university are collaborating on a $2.3 million grant from the National Institute for Occupational Safety & Health (NIOSH) to create mobile tools to monitor workplace chemical exposure—in particular for truck drivers who risk exposure to hazardous chemicals from exhaust fumes, cargo, and gases released during fueling.
The interdisciplinary team is using micro-GC technology to create a completely new form of personal protective equipment. “For some occupations where people may be exposed to dangerous chemicals, we don’t have real-time analysis,” says Agah. “This project tries to tackle that.”
Using conventional methods, exposure is measured by capturing data over periods of 6 to 12 hours, offering only a broad overview. The Virginia Tech researchers plan to change that, collecting near-term data that can be used to identify when and where the drivers are exposed, and what additional safety practices can help protect them.
The researchers are employing multiple technologies to optimize a micro-GC device they call the iWAVE (intelligent Wearable Analyzer for Vapor Exposure).
Each of us is exposed to thousands of chemicals daily. Most are harmless. Some are not. Knowing when we’re exposed to harmful chemicals is vital for workplace safety, but monitoring efforts are hampered by the large size of the technologies typically needed to detect these chemicals.
The gold standard for detecting what’s in the air we breathe is gas chromatography (GC)—an analytical method for determining the chemical composition of a gas using a device that runs gases through several meters of a capillary tubing known as a separation column. The size and expense of conventional GC equipment, however, present a challenge when trying to analyze in real-time, as does the time-consuming process of sending samples to a lab.
The solution, according to ECE Professor Masoud Agah, is a portable and/or wearable micro-GC, which combines a variety of different technologies. Over the last 17 years, his teams have made numerous advances to miniaturize GC technology and to develop new GC architectures. GC suitcase-sized equipment typically weighs 30 pounds or more. “We want to make something you can wear, without noticing the weight,” he says.
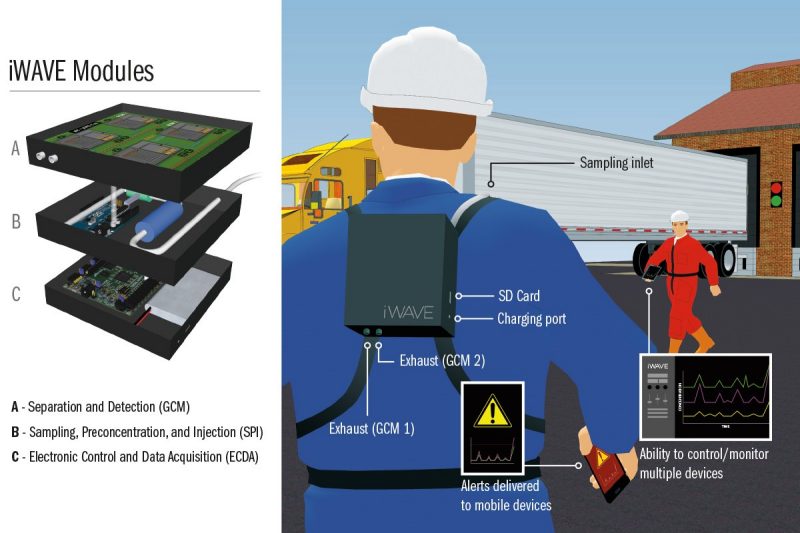
The iWAVE combines a number of technologies, including micro-electromechanical systems (MEMS) and semiconductor fabrication, embedded computing, microfluidics, machine learning, and 3D printing. The device provides near-real-time analysis of the environment surrounding the wearer—monitoring chemical exposure levels on the fly and flagging any dangers. “If you are exposed to acetone, it’s probably fine,” Agah notes. “If it’s benzene, that’s a different story.”
Crafting the iWAVE
Miniaturizing GC technology is not simple. iWAVE devices will perform the functions of an entire benchtop apparatus, process the data, and wirelessly communicate with cloud-based analytics. From microchips to electrical and fluidic connectors, pressure regulators to electronic and computing circuits, every step needs unique solutions to perfect the balance between efficiency, power, and size.
The current iteration of the device is built on student innovation, Agah explains. “A lot of what we have done in the lab are things the students bring to the table. They don’t give up. For some of the students it took two years to get past the first barrier, but eventually they succeeded.”
With the new iWAVE devices, the researchers will train cloud-based machine learning algorithms to detect dangerous compounds, and inform safety policies of the future.
Beyond the workplace
But the applications do not stop there. This technology can translate chemical compounds in the air into a digital signature—expanding our understanding of our environment and surroundings. The iWAVE and micro-GC could open new avenues to evaluate personal health through breath and skin odor analysis, check food safety, search for signs of life during natural disasters, detect diseased plants, and maybe even take a “scent snapshot,” capturing the chemical signals of a fragrance you love, Agah suggests.
For now, the iWAVE is focused on monitoring high risk environments to ensure the safety of otherwise hazardous occupations. But Agah has high hopes for this technology moving forward, saying that this is a platform that can revolutionize many different industries. He and his students and colleagues are ready to tackle the challenges.